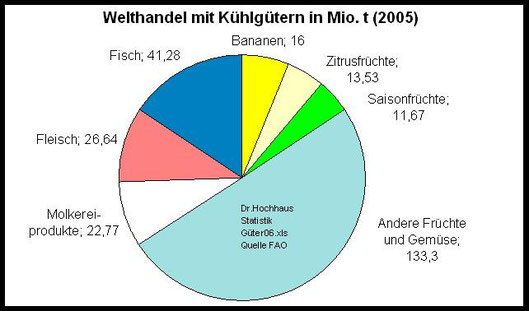
Bild 1: Der Welthandel von Kühlgütern betrug 2005 rund 265 Mio. t und teilt sich in 7 Gruppen auf, in Fleisch, Fisch, Bananen, Saisonfrüchten, Molkereiprodukten, Gemüse und andere Kühlgüter (Datenquelle FAO).
Der Transport von Kühlladung über See ist 2002 auf insgesamt 63 Mio. t gewachsen. Der Transport von rund 70 Mio. t Kühlgüter wurde 2005 etwa zu je 50 % von Kühl- und
Containerschiffen durchgeführt, obwohl letztere mit 816 Mio. cbft im Vergleich zu den Kühlschiffen mit 336 Mio. cbft mehr als das Doppelte an Kühlkapazität haben.
Anfang 2006 wurden die EU-Handelsbeschränkungen für Bananen aufgehoben und in ein reines Zollsystem überführt.
Dieser Beitrag wurde 2006 in der Deutschen Verkehrszeitung veröffentlicht
Kühlladung und
Container
Karl-Heinz
Hochhaus
Einführung
Die Kühlcontainer haben seit ihrer Einführung vor rund 50 Jahren die Kühlräume der Linien-Frachter ersetzt und seit dem Bananenkrieg zwischen der EU und der USA 1993 wird auch die Konkurrenz mit
den Kühlschiffen immer deutlicher wahrgenommen. Seit 1966 wurden mehrere Innovationsschritte in der Kälte- und Automationstechnik absolviert, die vom isolierten Container
(Porthole-Container) ohne eigenes Kälteaggregat bis zum heutigen automatischen Integral-Container geführt haben.
Damit wurde der 2005 abgeschlossene Übergang der Nord-Süd-Fahrtgebiete vom Porthole- zum Integralcontainer möglich, der jedoch durch einen erhöhten Energieverbrauch und aufwendige Überwachung
erkauft wird. Der Kühlcontainer beinhaltet den Vorteil einer geschlossenen Kühlkette und ermöglicht den preiswerten Transport und Verteilung kleiner Mengen an Kühlla-dung im intermodalen Verkehr.
Die in einigen Containern realisierte MA- und CA-Technologie hat den Wettbewerb zur Luftfracht bei sensiblen Früchten belebt.
Kühlladung
Der Welthandel von Kühlgütern hat sich von 204 (1995) auf 247 Mio. t (2002) gesteigert, der Transport von Kühlladung über See hat sich im gleichen Zeitraum um 32 % erhöht und ist 2002 auf
insgesamt 63 Mio. t gewachsen. Fleisch lag mit 16,9 Mio. t vorn, gefolgt von Fisch (13,9 Mio. t), Bananen (12,7 Mio. t), Saisonfrüchten (7,3 Mio. t), Zitrus (6,9 Mio. t), exotischen Früch-ten
(3,7 Mio. t) und Molkereiprodukten (1,9 Mio. t). Ostasien ist vor den USA mit 29,5 % der wichtigste Markt. Das Wachstum hat auch von 2003 bis 2005 in etwa gleicher Größenordnung angehalten und
wird weitgehend von der gestiegenen Nachfrage in Russland und Ostasien getra-gen. Anfang 2006 wurden die EU-Handelsbeschränkungen für Bananen aufgehoben und in ein reines Zollsystem überführt.
Die daraufhin gefallenen Preise haben den Bedarf nach Kühlraum erhöht und können aufgrund von Engpässen bei Kühlschiffen für steigende Raten sorgen, da Bananen als typische Ladung für Kühlschiffe
schon bisher für 30 bis 40 % der Beschäftigung sorgen.
Der Transport von rund 70 Mio. t Kühlgüter wurde 2005 etwa zu je 50 % von Kühl- und Containerschiffen durchgeführt, obwohl letztere mit 816 Mio. cbft im Vergleich zu den Kühl-schiffen mit 336
Mio. cbft mehr als das Doppelte an Kühlkapazität haben. Bezogen auf die Kühlkapazität der Kühlcontainer mit rund 1,2 Milliarden cbft wird das Verhältnis noch schlech-ter, denn jeder Kühlcontainer
wird im Mittel nur zwei- bis dreimal pro Jahr genutzt.
Kühlcontainer
Derzeit sind rund 1,25 Mio. TEU Kühlcontainer im Markt, etwa 900.000 TEU gehören den Reedereien, Maersk Line besitzt mit rund 300.000 TEU mit Abstand den größten Anteil. Die Fertigung stieg in
der Vergangenheit jährlich um rund 10 % und lag 2005 bei rund 90.000 Ein-heiten (ca. 170.000 TEU). Nach Aussagen von Fachleuten werden 2006 erstmals weniger Kühl-container als im Vorjahr
hergestellt. Die heutige globale Produktion der Kühlcontainer erfolgt zu etwa 80 % in China, China International Marine Containers (CIMC) und Maersk Container Industries (MCI) sind die
bedeutendsten Hersteller von Kühlcontainern. MCI, die neben China auch in Dänemark fertigen, verlagern die dänische Produktion Anfang 2007 ebenfalls nach China.
Es wurden erhebliche F- und E-Arbeiten durchgeführt, damit die Haltbarkeit, das Leerge-wicht, die Isolierung und die Dichtigkeit den hohen Anforderungen des Seetransports, des Ha-fenumschlags und
des Straßen- und Bahntransports entsprechen. Gefordert werden in der Norm ISO 1496 z. B. das max. Stapelgewicht von 96 t, die Wärmedurchgangsrate von 51 W/K und das max. Einzelgewicht pro
Container von 30,4 t. Zur Kälteerzeugung haben sich Kolbenverdichter bewährt, sie werden jedoch zunehmend von den kostengünstigeren Spiralverdichter (Scroll) verdrängt. Als Vorteile der
innovativen Scroll-Verdichter gelten besonders das niedrigere Ge-wicht und das geringere Geräuschniveau. Weitere Optimierungen und Anpassungen sind jedoch notwendig, um den E-Verbrauch der
Kühlcontainer und der Laderaumlüftung zu senken.
MA-CA-Technologie
Die aus der Langzeit-Fruchtlagerung bekannte Technologie der „Kontrollierten Atmosphäre“ (MA/CA auch) wurde
ab Mitte der 90ger Jahre in die Transporttechnik übernommen. Dabei wird nicht nur die Temperatur sondern zusätzlich der Sauerstoffgehalt der Laderäume auf niedrige Werte von 2 – 5 % abgesenkt,
zuerst auf Kühlschiffen und bald darauf im Kühlcontainer. Damit wird der Stoffwechsel der Früchte reduziert, dies ist beim Transport der klimakteri-schen Früchte wie z. B. Bananen von großem
Vorteil.
Die technologisch einfache Methode der Selbstveratmung wurde z. Bsp. als „Automated Fresh Air Management“ (AFAM-System) von THERMO KING (USA) in den Markt eingeführt. Je nach Dichtigkeit der
Container, Art, Zustand und Anfangstemperatur der Früchte kann die Sauerstoffreduzierung nach 2 bis 3 Tagen abgeschlossen sein (MA).
Im Gegensatz dazu steht das „Tectrol“-System der Firma TRANSFRESH (USA), das die Luft im Container nach der Beladung mit einer Gasmischung ausspült und ersetzt. Der CO2-Gehalt wird durch einen
CO2 –Scrubber reduziert. Dies System benötigt eine externe Logistik bzw. Niederlassungen in den Ladehäfen und ist daher nur eingeschränkt verfügbar.
Technologisch anspruchsvoller sind das „Cargofresh“-System der Firma CARGOFRESH (Deutschland) und die MA/CA-Systeme „Autofresh“ und „Everfresh“ von CARRIER (USA), die mit im Kühlcontainer
integrierten Stickstofferzeugern arbeiten. Hier wird der im Container- Innenraum befindliche Luftsauerstoff und die Atmungsprodukte der Früchte wie Kohlendioxyd und Ethylen durch den Stickstoff
verdrängt und eine modifizierte bzw. kontrollierte Atmosphäre ermöglicht.
Containerüberwachung
Die Porthole-Technlogie ermöglichte eine ideale Überwachung der Kühlcontainer. Auf Schiffen mit wenigen Integral-Kühlcontainern genügt die manuelle Überwachung durch die Besatzung. Die
traditionelle Technik zur Container-Fernüberwachung erfolgt durch ein vierpoliges Kabel, welches zusätzlich zu dem Stromkabel angeschlossen wird.
Auf Containerschiffen mit vielen Kühlcontainer-Steckdosen erfolgt die Überwachung durch das Stromkabel (PCT=Power Cable Transmission). Dafür werden im Container und Schiff Modems
installiert, die zur Dateneinspeisung und Auslesung benötigt werden. Rund zwei Drittel aller neuen Kühlcontainer werden derzeit entsprechend ausgerüstet. Etwa 40 – 45 % der existie-renden
Kühlcontainer sind derzeit für die PCT-Technik auf dem Schiff oder Terminal zu ausge-rüstet.
Die speziell für den Südamerikadienst konstruierten 5500 TEU Schiffe der MONTE-Klasse verfügen mit 1365 Kühlcontainer-Steckdosen, das sind rund 2.700 TEU, über die weltweit größte
Kühlraumkapazität. Pro Steckdose benötigt die Reederei etwa drei Kühlcontainer, das sind 4100 Kühlcontainer, die bei heutigen Preisen von 18.000 $ mit insgesamt 74 Mio. $ teurer sind als die
Schiffe.
Erläuterungen und Abkürzungen
Integral-Container:
Isolierter Container mit integrierter vollautomatischer Kälteanlage, die elektrisch angetrieben wird. Der Anschluss erfolgt an das elektrische Netz des Schiffes oder des Hafens, auf dem Schiff stehen die Integral-Container überwiegend an Deck.
Porthole-Container:
Isolierter Kühlcontainer, der an einer Stirnseite zwei Öffnungen zum Andocken an einen Kühlluftkanal besitzt. Der schiffsfeste Kühlluftkanal befindet sich im Laderaum und ist in einen Zu- und einen Abluftkanal unterteilt. Die Kälteanlage befindet sich im Gegensatz zum Integralcontainer im Schiff.
Abkürzungen
BRT = Bruttoregistertonnen
TEU = Twenty Foot Equivalent Unit (20 Fuß Containereinheit)
R-TEU = Reefer TEU (20 Fuß Kühlcontainereinheit)
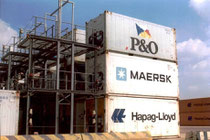
Bild 4: Kühlcontainer im Hafen, auch hier erfolgt der Anschluss an die elektrische Energie-versorgung und eine regelmäßige Kontrolle (Foto Dr. Hochhaus)